Introduction
DC motor controllers are essential components used in a wide range of applications, from robotics and automation to electric vehicles. As a beginner in the world of electronics and engineering, understanding the fundamentals of DC motor controllers is crucial to harnessing their full potential. In this comprehensive guide, we will delve into the basics of DC motor controllers, their types, functionalities, and practical applications.
1. What is a DC Motor Controller?
A DC motor controller is an electronic device designed to regulate the speed and direction of a DC motor. It acts as an intermediary between the power supply and the motor, allowing precise control over its rotation and movement. By altering the voltage and current supplied to the motor, DC motor controllers enable smooth and efficient operation.
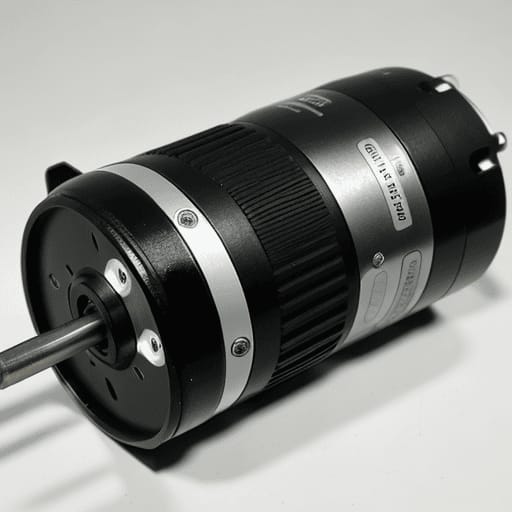
2. Types of DC Motor Controllers
There are several types of DC motor controllers, each catering to specific applications and requirements:
a. On/Off DC Motor Controllers: These controllers simply turn the motor on or off, providing basic control but limited speed regulation.
b. Pulse Width Modulation (PWM) DC Motor Controllers: PWM controllers rapidly switch the power supply on and off to the motor, varying the duty cycle to control the motor speed.
c. H-Bridge DC Motor Controllers: H-Bridge controllers allow bidirectional control of the motor by using four switches to control current flow through the motor windings.
d. Brushed DC Motor Controllers: Designed for traditional brushed DC motors, these controllers offer simple and cost-effective speed control solutions.
e. Brushless DC Motor Controllers (BLDC): Ideal for brushless motors, these controllers provide smooth and efficient speed control with improved reliability.
3. How Do DC Motor Controllers Work?
DC motor controllers use various control techniques to regulate motor speed and direction. PWM controllers change the duty cycle of the input voltage, while H-Bridge controllers reverse the current flow to change the motor’s rotation direction. Advanced controllers may utilize feedback mechanisms like encoders or hall-effect sensors to maintain precise speed and position control.
4. Choosing the Right DC Motor Controller
Selecting the appropriate DC motor controller depends on factors such as motor type, voltage, current requirements, and the desired level of control. Consider the specific application, power demands, and budget constraints when making your choice.
5. Practical Applications of DC Motor Controllers
DC motor controllers find applications in numerous fields, including:
a. Robotics: Used to control robotic arms, autonomous vehicles, and humanoid robots.
b. Electric Vehicles: Facilitating speed regulation in electric cars, bikes, and scooters.
c. Home Automation: Controlling motorized curtains, blinds, and fans.
d. Industrial Automation: Driving conveyor belts, assembly line machines, and automated processes.
e. Electronics Projects: Controlling propellers, wheels, and various mechanical components.
6. Tips for Safe and Efficient Use
When working with DC motor controllers, it’s essential to follow safety precautions to prevent accidents and protect the equipment. Ensure proper grounding, use appropriate current and voltage ratings, and avoid overloading the controller to ensure smooth and efficient operation.
In the end, Understanding DC motor controllers is a crucial step for anyone venturing into the world of electronics and robotics. With this guide, you now have a solid foundation to comprehend the different types of DC motor controllers, their functionalities, and how to select the right one for your projects. Whether you’re a hobbyist or an aspiring engineer, mastering DC motor controllers will open up a world of possibilities for your future projects and innovations. Happy experimenting!
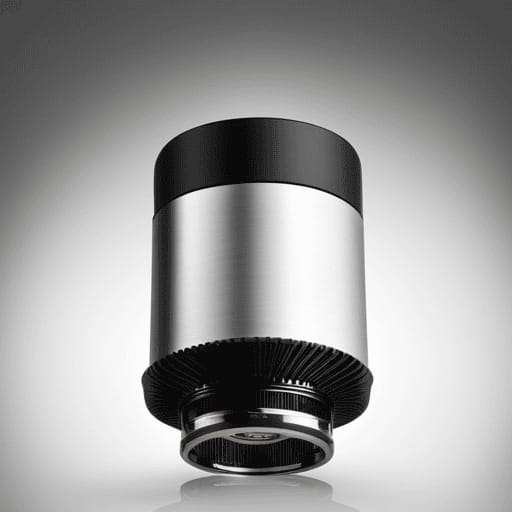
Exploring the Latest Trends in DC Motor Controller Technology
Introduction:
DC motor controllers play a vital role in various industries, ranging from robotics and automation to electric vehicles and industrial machinery. Over the years, advancements in technology have led to significant improvements in DC motor controller designs, resulting in more efficient, precise, and reliable motor control solutions. In this blog post, we will explore the latest trends in DC motor controller technology, shedding light on how these innovations are shaping the future of motor control.
1. Brushless DC (BLDC) Motor Controllers:
One of the most prominent trends in DC motor controller technology is the widespread adoption of Brushless DC (BLDC) motor controllers. BLDC motors offer several advantages over traditional brushed DC motors, including higher efficiency, reduced maintenance needs, and longer lifespan. The latest BLDC motor controllers integrate advanced control algorithms, enabling smoother operation and precise torque control for various applications like drones, electric vehicles, and industrial machinery.
2. IoT-enabled Motor Controllers:
Internet of Things (IoT) technology has made its way into the realm of DC motor controllers, enabling remote monitoring, control, and diagnostics. IoT-enabled motor controllers allow real-time data collection, which can be used for predictive maintenance, performance optimization, and energy efficiency analysis. These controllers are ideal for industries where automation and remote access are crucial, such as smart manufacturing and home automation.
3. Sensorless Motor Control:
Traditionally, motor controllers required feedback from sensors like encoders or Hall-effect sensors to determine the motor’s position and speed accurately. However, sensorless motor control has emerged as a trend that eliminates the need for these external sensors. Advanced algorithms and motor modeling techniques enable motor controllers to estimate the motor’s position and speed based on the current and voltage measurements. Sensorless motor control simplifies the design and reduces costs, making it a compelling option for various applications.
4. Regenerative Braking:
Regenerative braking is a concept that has gained significant traction in electric vehicles and robotics. It involves converting the kinetic energy generated during braking back into electrical energy and storing it in a battery or capacitor. Modern DC motor controllers with regenerative braking capabilities not only improve energy efficiency but also extend the battery life in electric vehicles, thus enhancing overall performance.
5. High-Frequency PWM Control:
The adoption of high-frequency Pulse Width Modulation (PWM) control in DC motor controllers is becoming more prevalent. High-frequency PWM minimizes acoustic noise and reduces motor vibration, resulting in quieter operation and smoother motion. Additionally, it helps to reduce switching losses, leading to improved efficiency in motor control systems.
6. Integrated Motor Drivers:
The integration of motor drivers with microcontrollers or application-specific integrated circuits (ASICs) is a trend that simplifies system design and reduces component count. Integrated motor controllers offer a compact solution with improved thermal performance and lower overall system cost. These controllers find applications in battery-powered devices, robotics, and portable consumer electronics.
In the end, The latest trends in DC motor controller technology are driving innovation and efficiency across various industries. From the adoption of BLDC motor controllers for electric vehicles to the integration of IoT and sensorless control, these advancements are reshaping the future of motor control systems. As technology continues to evolve, we can expect even more sophisticated motor controllers with improved performance and enhanced features, enabling a wide range of applications to benefit from efficient and precise motor control.
Top 5 Best DC Motor Controllers for Robotics Projects
Introduction:
1. Pololu Dual VNH5019 Motor Driver Shield:
The Pololu Dual VNH5019 is a powerful motor driver shield designed for Arduino and compatible microcontrollers. It can drive two high-current DC motors or a single bipolar stepper motor, making it ideal for small to medium-sized robotics projects. The shield provides efficient current sensing and protection against overcurrent and overheating, ensuring reliable performance.2. Adafruit Motor/Stepper/Servo Shield:
Adafruit’s versatile Motor/Stepper/Servo Shield is perfect for robotics enthusiasts working with Arduino boards. It can control up to four DC motors or two stepper motors with precise speed and direction control. Additionally, it includes connections for up to two servos, making it an excellent choice for robotic arms and other servo-driven mechanisms.3. L298N Dual H-Bridge Motor Driver:
The L298N is a popular and affordable dual H-bridge motor driver module. Although it requires external components, it offers robust functionality and is widely used in robotics projects. It can drive two DC motors bidirectionally and handle currents up to 2A per channel. This motor driver is compatible with various microcontrollers, making it a versatile choice for DIY robot builders.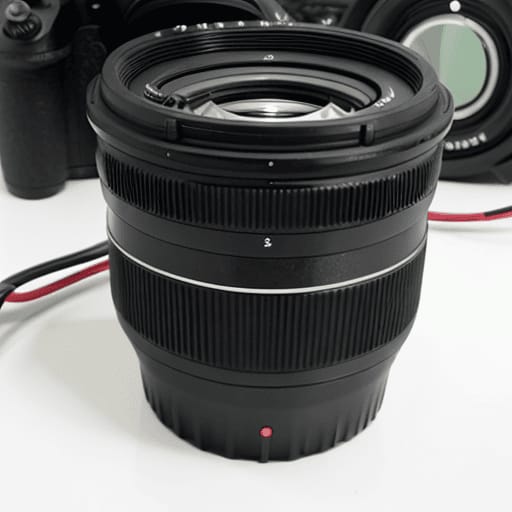
RcLC EoQ lXFqaI